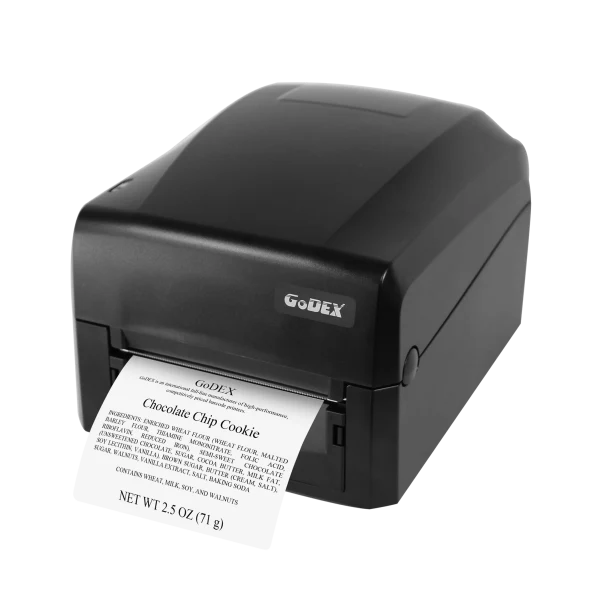
For businesses that rely on consistent shipping, a properly set-up shipping label printer can boost productivity and streamline order fulfilment. Here’s a step-by-step guide to setting up and optimising your printer for maximum efficiency.
1. Choose the Right Shipping Label Printer
Before setting up, ensure you have the right printer for your needs. Thermal printers are ideal for high-volume printing as they don’t require ink, reducing running costs. CDM Labels offers a variety of shipping label printers, making it easy to find one that suits your business needs.
2. Initial Setup and Software Installation
Once you’ve selected a printer, install any software drivers or configuration tools that accompany the printer. Many printers also come with label design software, making it easier to customise labels with your logo, address, or shipping instructions.
- Connecting the Printer: Connect the printer to your computer via USB, Bluetooth, or Wi-Fi, depending on your model’s connectivity options. Make sure the connection is stable, especially for wireless options.
- Driver Installation: If the drivers aren’t pre-installed, download them from the manufacturer’s website to ensure compatibility with your operating system.
3. Loading the Labels Correctly
Loading the labels correctly is essential to avoid printing errors or jams. Open the label compartment and position the labels according to the manufacturer’s instructions. Some printers have guides that help align labels precisely, ensuring each label prints in the same spot every time.
- Choose Label Size: Check that your label size matches your printer settings to avoid misprints or wasted labels.
- Adjust Printer Settings: Set the printer’s configuration (e.g., label width, length, and feed direction) for the label size you’re using.
4. Calibrate Your Printer
Calibration ensures each label prints correctly and within the label’s bounds. Most label printers have a calibration function that lets the printer identify the beginning and end of each label. Run the calibration test periodically to prevent print alignment issues, especially when changing label types or sizes.
5. Optimising Print Quality and Speed
Ensuring that your labels are printed clearly and at the right speed makes them easier for carriers to scan, reducing issues in transit. Adjust print settings to the optimal DPI (dots per inch) for clear barcodes and text. Higher DPIs give clearer labels but can slow down printing, so find a balance that meets your needs.
- Set Print Density: Many printers allow you to adjust the density to make the text or barcodes bolder or lighter. Set it to a level that makes labels easily scannable.
- Optimise Print Speed: If you’re handling large volumes, consider setting a faster print speed to save time, though this may reduce clarity slightly on some models.
6. Integrating with Shipping Software
Integrate your shipping label printer with your preferred shipping software for seamless printing. Many platforms, like ShipStation or Shopify, support direct label printing and provide templates, making it easier to print labels with minimal input.
- Connect Directly to Online Marketplaces: Many online marketplaces, such as eBay or Amazon, allow integration with shipping label printers. This automates the label printing process and reduces the risk of input errors.
- Batch Printing: If you’re fulfilling multiple orders daily, use batch printing features in your shipping software to print multiple labels at once.
7. Regular Maintenance and Cleaning
Regularly clean your printer, particularly if using a thermal printer, to prevent dust build-up that can impact print quality. Many thermal printers come with cleaning kits, which may include a soft cloth and cleaning swabs. Regular maintenance prolongs the printer’s lifespan and keeps print quality high.
- Clean the Printhead: The printhead accumulates dust and adhesive from labels. Use a printhead cleaning pen or isopropyl alcohol to clean it gently.
- Check for Label Build-Up: Sometimes, bits of adhesive from labels stick to rollers or guides. Inspect these areas frequently and remove any build-up.
8. Use High-Quality Labels
Quality labels contribute to better printer performance and ensure labels are durable during shipping. Invest in labels designed for your printer model to prevent feed and adhesion issues.
- Weatherproof Labels: For businesses shipping internationally or in harsh conditions, opt for weatherproof or waterproof labels, which are more resistant to smudging and tearing.
- Avoid Low-Cost, Poor-Quality Labels: Lower-quality labels may peel or cause jams, leading to wasted time and resources.
9. Troubleshooting Common Issues
Having a checklist of common troubleshooting steps can minimise downtime if issues arise. Here are some quick fixes:
- Print Misalignment: If labels print off-centre, recalibrate the printer or check that the label size in the settings matches the loaded labels.
- Blank Labels: If your thermal printer is printing blank labels, the issue could be a low battery (for portable models), a disconnected cable, or an incorrect print setting.
- Error Messages: Refer to the user manual or manufacturer’s website for error code explanations and solutions.
10. Monitor Ink or Thermal Paper Usage
If your printer uses ink, monitor ink levels to ensure uninterrupted printing. For thermal printers, keep a supply of thermal paper handy to prevent running out during high-demand periods. Many businesses keep spare supplies on hand to avoid delays.
Conclusion
Setting up a shipping label printer properly and optimising its settings can dramatically improve the efficiency of your shipping process. By following these steps and choosing the right supplies, you can enjoy seamless, high-quality label printing that supports your business’s productivity.
For a range of high-quality shipping label printers, check out CDM Labels.